Essential for the homogenization of materials, roll mill ensure optimum dispersion of components and have a direct impact on the quality of finished products.
A more general article on the mixing process is available on our blog!
What is a roll mill?
A roll mill is an essential piece of industrial equipment for processing polymers, especially rubber. It consists of two parallel rolls rotating in opposite directions, used to mix, homogenize and prepare compounds for further processing. These machines are widely used in the rubber, silicone and plastics industries to ensure uniform dispersion of components and improve the quality of finished products.
Roll mill structure and components
Typically, a roll mill comprises :
- Rotating cylinders : Two steel cylinders, arranged horizontally and rotating in opposite directions. The cylinders are hollow or perforated at the periphery to allow fluid circulation, ensuring precise temperature control during the mixing process
- Gap adjustment system: Mechanism for adjusting the distance between cylinders to control the thickness of the material processed and the intensity of mixing.
- Drive mechanism: a set of motors and gearboxes that rotate cylinders at controlled speeds, often with a differential speed ratio to optimize material shear.
- Rubber limiters: Devices designed to direct the rubber mix between cylinders, ensuring uniform treatment of the material. They are placed at the ends of the cylinders to redirect the material towards the center and minimize losses.
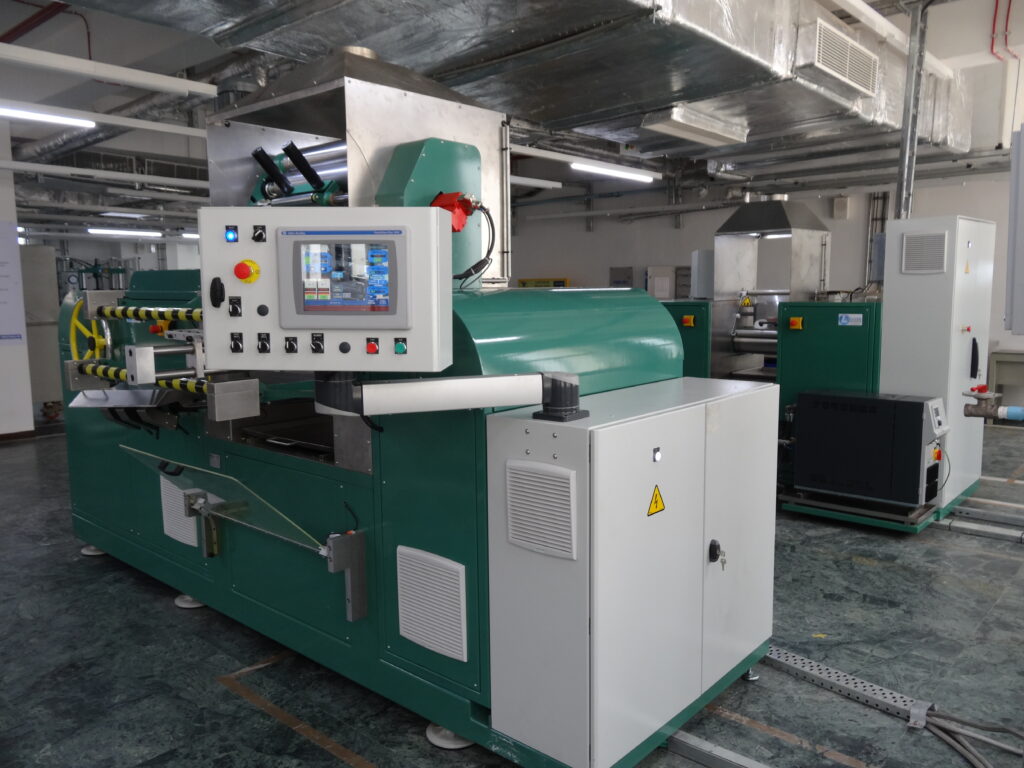
Operating principle
The operation of a roll mill is based on the following steps:
- Raw material feed: raw rubber or polymer is fed into the space between the two rotating cylinders.
- Mixing and homogenization: counter-rotating cylinders exert shear forces on the material, promoting uniform dispersion of additives and fillers. Controlling the temperature of the cylinders is crucial to maintaining mixing properties and avoiding thermal degradation. Typically, operators are tasked with mixing the material by hand, using a knife. However, some companies, such as Lescuyer & Villeneuve, have developed systems that automatically mix the material, without operator intervention.
- Parameter adjustment: The operator can modify cylinder spacing, rotation speeds and temperature to obtain the desired mixture characteristics.
- Blend extraction: Once the process is complete, the homogenized blend is removed in sheet or strip form, ready for subsequent processing steps such as extrusion or calendering.
This process produces high-quality blends, essential for the performance of finished products in a variety of industrial applications.
Types of Lescuyer & Villeneuve roll mill
Lescuyer & Villeneuve divides its production into two main types of equipment: production roll mill and laboratory roll mill.
Lescuyer & Villeneuve production roll mill
The Lescuyer & Villeneuve production roll mill is specially designed to meet the requirements of manufacturers working with polymers such as rubber and silicone. Adapted to high production volumes, it guarantees optimum batch homogeneity, while ensuring precise mixing control, particularly in the presence of heat-sensitive additives.
Equipped with cylinders from 300 to 750 mm in diameter and a table from 650 to 2,500 mm, this equipment can handle batches from 15 to 250 kg. Its exclusive electric motorisation, a unique innovation on machines of this size, eliminates the constraints of traditional hydraulics and offers advantages in terms of maintenance, environmental impact, gauge accuracy and safety.
L&V production roll mill features
Compliant with the most stringent safety standards (EN 1417:2023), this roll mill offers the following features:
- Electrical gap adjustment
- Peripherally drilled cylinders for improved material cooling
- Energy recovery system
- Innovative non-energy safety system
As an option, they can be completed with automated solutions, automatic mixing systems, blenders, knives, etc…
The Lescuyer & Villeneuve laboratory roll mill
Lescuyer & Villeneuve laboratory roll mill are specially designed for small quantities of material, offering an ideal solution for research and development. They enable new mixes to be tested, material behavior to be studied, and formulations to be optimized before going into industrial production.
Equipped with cylinders from 55 to 250 mm in diameter and a table varying from 150 to 500 mm, these machines handle batches ranging from 0.1 to 8 kg, while ensuring precise mixing control, including for additives. Their compact monoblock design optimizes footprint, making them easy to integrate into any laboratory or research center environment.
Ergonomics and ease of use are at the heart of their design, with an intuitive touch-sensitive control panel for precise parameter adjustment.
Features of the L&V laboratory roll mill
This equipment also complies with the most stringent safety standards (EN 1417:2023), and offers the following features:
- Electrical gap adjustment
- Peripherally drilled cylinders for improved material cooling
- Energy recovery system
- Customization options
Our laboratory roll mills work on rubber, silicone and plastics. In addition, options can be added, such as automated systems, automatic mixing systems, etc…
Nanomaterials mixer: a specific equipment
The Lescuyer & Villeneuve nanomaterial mixer is an innovative solution designed for the automated, confined mixing of materials enriched with nanomaterials. It meets the industry’s growing demands for safety and precision, particularly in the face of the challenges posed by nanoparticles.
The entire process is automated using a robotic arm and the Vomery automatic mixing system developed by Lescuyer & Villeneuve. This automation enables precise, controlled integration of additives, while optimizing blend homogeneity and guaranteeing operator safety.
Compact and powerful, this roll mill can be fitted with advanced instrumentation, including a thermal camera for real-time monitoring of temperature variations.
Like all Lescuyer & Villeneuve equipment, the nanomaterials mixer complies with the most stringent safety standards (EN 1417:2023) and can be customized to meet specific user requirements.
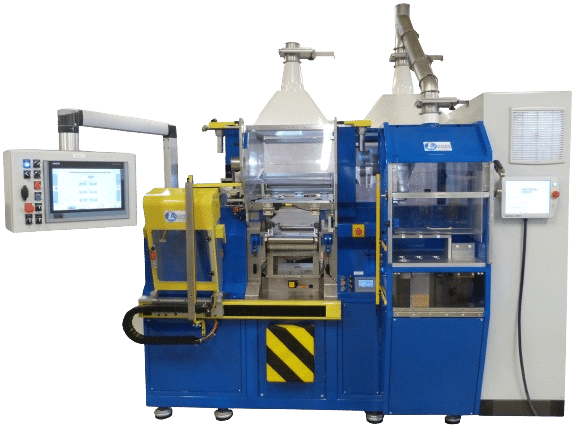
Conclusion
Roll mills are essential for homogenizing polymers such as rubber, silicone and plastics. Their robust, technological design optimizes material processing.
Lescuyer & Villeneuve offers solutions tailored to industrial needs: a high-performance production roll mill for large volumes, a laboratory roll mill ideal for research, and an innovative, safe nanomaterials mixer. This modular, safety-compliant equipment improves manufacturing processes and the quality of finished products